Applied Engineering Supports Booming Alabama Industry
10/17/2018
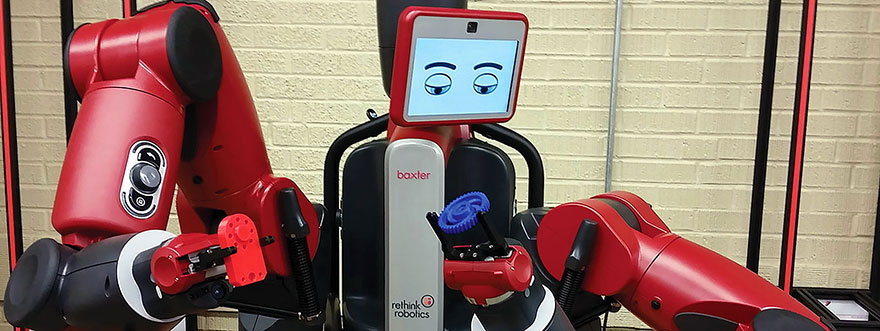
By Brett Buckner
The Department of Applied Engineering has an unofficial motto: “Anyone who wants a job, gets a job.”
More than 94 percent of applied engineering graduates find work in their chosen field, though the actual number is higher, explained Chris Marker, interim department head.
“We could advertise that the employment rate is really over 100 percent because a lot of our students get hired as juniors and seniors,” Marker said. “Our students are often out and working even before they graduate, but we don’t advertise that because it sounds unbelievable.”
In applied engineering, students learn by doing. All programs are designed for hands-on application. Students are working with the latest manufacturing technology in order to better apply concepts in real-world work environments.
“Our students are taught how to use the latest industrial technology,” Marker said. “Where traditional engineers are designing new technologies, our students are learning to use the newest technologies.”
Applied engineering graduates have secured jobs in a wide range of fields, including:
• Automation engineering
• Manufacturing engineering
• Production engineering
• Process engineering
• Development engineering
• Project engineering
• Design engineering
• Production supervising
• Maintenance supervising
At JSU, the goal is not only educating the next generation’s industrial workforce, but also keeping those future engineers close to home.
“Our big difference is that we are a regional investment, meaning that many in our program want to stay in the area and work for regional manufacturers,” Marker said. “That’s not always the case with more traditional engineering programs. Often times, students at Auburn or Alabama come from out of state, graduate and the leave the state. Most of our students stay here.”
Joy Pinckard is such a student. The 19-year-old applied manufacturing engineering major has been living in Jacksonville for five years. She moved here when her mother, Donna Perygin, got a job as a chemistry professor at JSU. It was around that time, when she was 14, that Pinckard discovered her interest in technology, especially robotics.
“I would build small robots with an Arduino – a popular, inexpensive programmable circuit board – and toy car motors,” she explained. “Soon after that I took up programming. I enjoyed it so much that I decided to make a career out of it.”
Pickard’s story is common among applied engineering students. While not all may have a passion for robotics, inspiration can come from anywhere, Marker said.
“We get students who love working with their hands, who like to build things, love computers or just want to understand how things work,” he said. “Even those who grew up playing games like Minecraft, will find out that they’ll fit right in with our engineering program.”
Center for Manufacturing Support
Applied engineering students are not simply building a future for themselves, but for the entire region. By encouraging graduates to stay close to home, the department has forged mutually beneficial relationships.
Students enter the program with the promise of a career in manufacturing and engineering, thus providing local businesses with a pipeline of potential employees who already have hands-on experience with the machines they’ll be using. The epicenter of this cooperative is JSU’s Center for Manufacturing Support, which serves as a proving ground for future applied engineering students and a testing site for regional industries looking to become more efficient.
Having officially opened in 2016, the center provides manufacturers with services ranging from design and prototype development to research and education – all while providing applied engineering students with job opportunities. What began as a pilot program two years ago has already outpaced expectations, Marker said.
“We thought this could be significant, but the feedback has already been better than we’d hoped for,” he said. “It’ll take a couple of years to build the program up, but already our biggest problem has been keeping up with the demand.”
The center has been successful on two fronts – as a boost to local economic development and as a source of pride for the university.
“JSU, on numerous occasions, has helped us tip the scales and bring in industry…we already use and tout the applied engineering school there quite a bit,” Don Hopper, executive director of the Calhoun County Economic Development Council, told the Anniston Star in October 2016. “This is another opportunity to sell the area as well work with existing businesses.”
Companies can use the center with minimal cost. It’s the students who do most of the work, providing them with experience and opportunity to network with potential employers.
“We’re putting the students in front of the people who will be hiring them,” Marker said. “It’s a lot different than when I was in school and we learned everything from a book. This gives students so much more confidence. They already know they can do the work.”
The accomplishments within the applied engineering department and the reputation those accomplishments have built within the industry are especially meaningful for Marker, who could be described as a JSU lifer. He received both his undergrad and graduate degrees from JSU. His father and sister are JSU professors. Before coming on full-time and eventually as interim department head, he was an adjunct professor teaching night classes. He’s also been out in the real world, having spent 17 years at Alabama Laser.
“I’m happy to give back to JSU because JSU has given so much to my whole family,” he said. “It was like coming home. Of course, I never really went away.”
Meet Baxter
As if being a catalyst for regional economic growth weren’t enough, the applied engineering department’s Robotics Team has also built a strong reputation for itself. Since its inception, the JSU Robotics Team has won the national title at the annual Association of Technology, Management and Applied Engineering Student Robotics Competition two out the five years it has competed. The team most recently took home first place in November 2015 at the competition in St. Louis, Mo.
“It’s really something to be proud of,” Marker said. “They’re going out there, competing against programs that have been around for 30 years and winning.”
All those trophies and accolades have practical purposes as well, like honing those competitive skills for on-the-job training with industrial robots like Baxter. Yet Baxter is unlike any robot you’ve ever seen. He is a “new generation” robot called a co-bot – or collaborative robot – because he is designed to work safely alongside humans, like an actual co-worker. Baxter’s design is intuitive, allowing for ease of programming.
“Baxter has a built-in safety system that detects when it has collided with anything – for instance, a person,” said Pinckard, who has worked with programming the co-bot. “That way if Baxter is swinging its arm around and it makes contact with someone or something that isn’t supposed to be there, it will stop moving immediately. I’ve tested this myself and it works very well.”
Baxter is not programmed in the traditional sense. Instead, he is trained.
“In other words,” Pinckard said, “To train Baxter to pick up a box, you would literally hold its hand and guide it through the motions. It’s considered a collaborative robot because it can be trained by someone without any programming experience.”
Baxter should pique the interest of students looking to study robotics.
“Ease of training makes Baxter accessible to new and future students who are unfamiliar with programming languages,” Pinckard said. “Because it’s safe to work around and intuitive to train, Baxter is an excellent tool for guiding future engineers to our program.”